DIY Speakers

1.0: Full Range Bass-Reflex speaker
These are the first set of high fidelity speakers built at the home shop. They use Fostex full range drivers and the 18-liter bass-reflex recommended enclosure.
-
Walls are 20 mm plywood, damped with 20 mm acoustic foam
-
Baffle is 20 mm solid cedar hardwood
-
Bass port is front-firing, PVC tubing with ID 65 mm coated with cedar veneer coating
Building process:







Finished product:


2.0: Titanium 2-way speakers
These speakers were intended for a flatter response, using low cost components such as a 6.5" ETM woofer in a bass-reflex enclosure and a titanium dome tweeter.
-
Walls are 15 mm plywood, damped with 20 mm acoustic foam
-
Baffle is 30 mm plywood
-
Bass port is bottom-firing, 4 mm PVC tubing with ID 65 mm
-
Due to port location, tall spikes were installed to ensure good airflow
-
Structure is reinforced to increase stiffness in all 3 axis

Titanium sound system presentation at HackPUC Maker Exposition 2017


Building process:











Components:
Woofer: ETM Alto Falantes EG-102S 6.5"
Tweeter: Dayton Audio DC25T-8 1" Titanium
Crossover: Dayton Audio XO2W-3K
Input Cups: DB-CUPS (3.15" x 3.15")
Spikes: 304 stainless machined at home.

Finished product:


3.0: Northern 2-way speakers
This set was designed from the start using high-end components, in order to achieve better sound quality than the 2.0 set.
-
Walls are 20 mm curve-laminated marine-grade MDF.
-
Baffle is 30 mm plywood
-
Bass port is front-firing, double-flanged 50 mm.
-
Both woofer and tweeter are ScanSpeak drivers made in Denmark.
-
Crossovers were custom built for the drivers by Madisound.
Presented at Rio de Janeiro Maker Faire 2018, got the Blue Ribbon distinguished project award.

Building process:






































A moment of silence for the brave C-clamps who gave their lives to complete the audiophile mission






After a few days of sanding, gap-filling, more sanding and smoothing, the structure was finally ready to receive its clotinhg.
Burled mahogany is just beautiful !


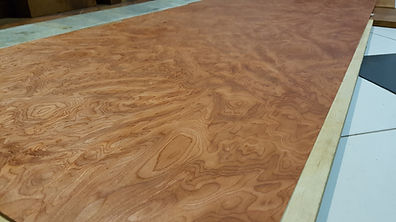

Since I could only find one single burled dark wood veneer sheet, this was a very delicate operation. We only had one shot at cutting the panels and aligning everything correctly. For that we cut cardboard frames to choose which patterns would be visible at each speaker wall. Contact glue was chosen to minimize the risk of ripping the thin veneer.






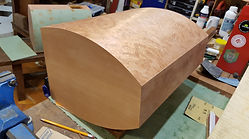


And finally, the varnish said: "Let there be wood !" And there was wood.





Time for some dampening using medium-density acoustic foam and automotive adhesive thermal blankets.





Finished product


In the words of Artemis Fowl :
More to Follow...